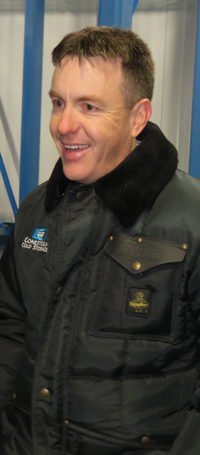
It’s minus 18 Celsius at the frozen heart of Conestoga Cold Storage’s Mississauga, Ontario facility, but Gavin Sargeant, the company’s vice-president responsible for automation, is warming to his subject.
Gavin Sargeant, Conestoga’s VP responsible for automation. (Photo: Emily Atkins)He’s showing a shivering group of supply chain and logistics professionals, all members of IWLA Canada, the newest addition to the site, a brand new ASRS that’s just days away from start-up. And although there’s no product being stored in the towering rack-supported building just yet, it is an engineering masterpiece.
The floor alone is a technical marvel with three feet of perfectly level concrete overtop of layers of gravel that overlays heating pipes needed to prevent permafrost forming under the perpetually frozen floor and heaving the building.
Conestoga is a family-owned cold storage and distribution operation founded in 1974. They offer warehousing, storage, blast freezing, case picking, and distribution services to the frozen food industry. The company prides itself on innovation and technical excellence.
That’s part of the reason why this facility was developed in 10 phases from 1995 to the present, each adding new technology and sophistication—culminating in the ultra-efficient ASRS systems—in an increasingly competitive cold storage marketplace.

Conestoga’s president Greg Laurin explained in a pre-tour briefing for the IWLA group: “Automation makes sense for cold storage for many reasons,” he said. “High land prices means going tall makes sense. High energy costs mean that the tall buildings are more efficient, and our biggest cost is labour, which we’ve been able to reduce by 70 percent because there’s nobody inside.”
The automation is also necessary to manage growth that’s been about 20 percent per year for the past 10 years, Laurin said. Overall, Conestoga has about 140,000 pallet positions in both conventional and automated temperature-controlled storage.
Another motivator for the company to stay ahead of the technology curve is customer demand. Already fully automated, with all orders coming through EDI and no paper trail, Laurin says customers request something new every day. The company offers batch number tracking, serial container number tracking (SSCC), GS 128 labels (for Loblaw), customized shipping labels (a Walmart request), automatic email notifications and more.
“It’s a challenge to drive it with software,” he says. “But it’s really a challenge to consistently meet the requirements of customers’ imaginations.”
Conestoga Snapshot:
Five facilities in Mississauga and Kitchener, Ontario, Calgary, Alberta and two in Montreal, Quebec.
Mississauga is the largest with:
• 45,000 sqf, 80,000 pallet positions and
25 million cubic feet
of storage space
• 100- and 120-foot-high ASRS storage
and 38-foot
clear conventional
cold storage
• 17 ASRS robots operating 24/7
• More than 300 trailers and 400,000 cases are handled every day

There seems to be a fair amount of imagination inside the company as well, judging by some of the projects that are underway at present. Sargeant explained how they are working with Egemin Automation out of the US to implement fully automated trailer-loading AGVs. Trials are currently underway and Laurin says the technology “may be a way to bring automation to a conventional cold storage building.”
Another project is a unique method of loading pallets into and out of the ASRS. The proprietary design is still under development and Sargeant—who designed it—requested we not describe it until it’s been operationally proven.
Conestoga has also built its own natural gas-powered generator that feeds energy back into the grid when it’s not required for the freezer operation.
A firm grasp on industry trends and challenges is one of the reasons that Conestoga is an industry leader in the cold storage business. Laurin highlighted the three main pain points in his presentation.

He first cited labour costs and the difficulty of recruiting tech staff. Cold Storage is “not Google, not sexy” he says, but as a highly automated business they have a huge need for programmers. On the labour side as well, he noted there is constant pressure from organized labour trying to expand in what is a heavily unionized business.
The second major challenge is government intervention. Too much regulation is “not beneficial to the employees or us,” he said. There is a significant cost associated with keeping up with regulatory changes, and the number of organizations the business must answer to is a significant source of frustration.
The final challenge is the cost of energy. Recent Ontario hydro price increases are hard to pass along to customers, he noted.
Leave a Reply