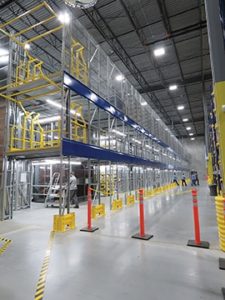
BMW Group Canada opened its new Regional Parts Distribution Centre in Mississauga, Ontario, this April, and Inside Logistics was invited in for a tour during the grand opening celebrations in June.
The new facility is 280,000 square feet, 50 percent bigger than the company’s old RDC located in the Whitby, Ontario, area. After 12 years, operations had outgrown capacity there, necessitating a move to a larger building.
Although the new RDC is no longer as convenient to the company’s Canadian HQ, which is in Markham, Ontario, the Mississauga location – on Argentia Road at the confluence of Ontario’s main 401 and 407 highway arteries – offers great transport links for product and employees, as well as a good pool of talent and a business-friendly environment, said Wolfgang Baumann, BMW Group’s vice-president of parts logistics management, in remarks at the opening.
Growth strategy
The three-storey mezzanine has 60,000 sq. ft. of storage. (Photo: Emily Atkins)The building was developed on a greenfield site by First Gulf, with groundbreaking in November 2016, and is managed for BMW Canada by 3PL Neovia Logistics. In addition to the existing space in use, there is room for another 64,000 sq. ft. to be added when needed. BMW Canada president and CEO Hans Blesse also noted there will be yet another new BMW parts DC coming in 2020 in the Vancouver, British Columbia, area.
The Mississauga DC is designed to support the company’s customer service commitment along with increasing efficiency in the parts supply chain, which is undergoing a global overhaul. “Canada is a unique market covering a large geographical area. We needed a modern distribution facility allowing us to deliver parts faster than our previous service offer,” Blesse said. “Faster deliveries mean less time away from your car and a more satisfying ownership experience – all top priorities for us.”
The DC serves 49 BMW and Mini retailers, as well as 24 Motorad (motorcycle) dealerships. With staffing of 52, it’s capable of handling more than 38,000 SKUs (of the approximately 400,000 available worldwide) and will be shipping more than a million parts a year. Everything, from complete engines to spark plugs, special bolts and body parts, moves through this facility.

The building sports a “nuclear-proof” 10-inch-thick concrete floor and is equipped with racking from North American Steel in a narrow-aisle configuration. The roof is 36 feet clear and the rack standard throughout the building is 28 feet, with extenders up to 30 feet on the aisle ends for safety. According to the facility’s manager, Ian Sant, there’s also a 60,000-square-foot mezzanine for small parts, with 60,000 bins locations over three levels. Almost 77 percent of the DC’s volume of 2,000 parts per day is picked from the mezzanine.
Planning makes perfect
A lot of planning went into the DC’s design. “We did a huge amount of planning in the foreground,” Sant said in an interview. Not only was the design team extremely experienced, he noted they left themselves about five months of buffer time in case of glitches.
“We ate up probably three months of it, but it still made that transition seamless. Combined, we’ve all opened a lot of warehouses together, so we understand what the problems are. I think that’s what made this so seamless, was that amount of preparation. It was two years in the making, so it gave us enough time to do that.”

All the material handling equipment is electric because it’s clean and safe, Sant said. “Propane’s dirty. It leaves a lot of sooty residue. The last thing we want to do is ship a part out to a customer and, you know, it’s got a layer of dust over it.” As well, BMW doesn’t want employees breathing all that dust.
“Electric is a lot easier to charge,” he adds. “You haven’t got that explosion risk of propane. They’re all opportunity charges – go on break, plug in, go for your lunch, you’re right by the lunchroom. Come back, your machine’s boosted and you can continue the operation.”
Quality control

As part of the company’s ethos as a purveyor of a luxury brand, there is a strong focus on quality. In the shipping area for large items like windshields, there is a pre-pack inspection station where each item is thoroughly examined for defects. Unacceptable items are set aside.
Because of the diverse size and nature of auto parts – everything from those windshields to bumpers, hoods to bolts moves through the DC – they stock over 80 different packaging types. Recently, an international team developed a new method for securing windshields that was shared at a BMW logistics conference and has now been adopted across the network. Neovia developed and maintains a thick paper-based manual that details exactly how each item should be placed into its protective distribution packing.

For the hoods the packaging team developed a special jig – built of commonly available plywood, carpeting and rollers – that allows the team to easily maneuver the hood into the box without fear of damaging it. Even the tiniest dent will mean rejection at the receiving end, so they are careful to ensure quality.
To ensure that the right parts are shipped out the DC employs RF scanning, double-checking the parts against the dealer manifest and that they are in the box for the correct dealer. The system is set up to trigger a loud alarm if the wrong item is picked or the wrong dealer box is selected, which, because it can’t be hidden from co-workers, is a strong incentive to get it right the first time, Sant said.
Going forward, he’s looking at other potential automation projects, including possibly using robotic carts. He wants to go see how one of the US operations is employing them before he decides, “but anything where we can look at engaging something that’s more futuristic, especially with the brand image,” Sant said. “We want to try and push that into gear.”
BMW By the Numbers
Outbound:
• 100% on time dispatch
• 4,000 lines shipped per day
• Orders drop by waves, 9 per day organized by route and order type.
• 5 carriers
• 23 different routes
• 2 daily courier deliveries in the GTA
• 4 overnight to Ontario retailers
• 1 overnight to Montreal retailers
• 1 overnight to eastern Ontario, Quebec, and eastern Canada
• 1 overnight to western retailers
• 2 overnight air shipments across Canada
Audit:
• 2,000 parts per day come from mezzanine to audit
• Audit checks part number matches pick label; quantity matches; part is defect-free
• Parts are scanned to specific dealer box
• When full, it’s moved to outbound where it is scanned onto dealer skid or cage as secondary audit.
Inbound:
• 1000 lines per day received
• 77,000 bin locations for putaway
• Inventory arrives from four main sources: Sea and airfreight from the central DC in Dingolfing, Germany; rush orders from the Regional DC in Nazareth, Pennsylvania; local suppliers in Canada
• Rush and Air freight to be confirmed into inventory day of receipt.
• Seafreight and stock to be confirmed within three days.
Leave a Reply