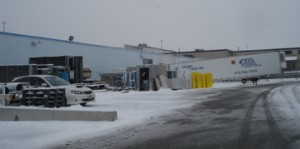
FROM THE MM&D MAY/JUNE 2012 PRINT EDITION:
As a professional engineer by trade, Suli Braunshtein brings a wide variety of technical skills and experience to his job as director of manufacturing and chief engineer at CMS Ontario Inc. These skills came in handy when the food producer decided to raise the roof.
CMS makes fruit and cheese fillings for its major customer, frozen food producer Fiera Foods Company. Toronto, Ontario-based CMS produces its fillings and stores them a 4,645sqm (50,000sqf) facility. Half of the building is devoted to manufacturing and half is warehouse space. Althoughthe manufacturing half is adequate for the company’s current production needs, the warehousing space had become tight.
This meant there were two options, move or renovate to increase the storage area. The company didn’t want to move, so Braunshtein started looking at ways to renovate.
“As a professional engineer, when I look at something, I think of it from an engineer’s point of view: how to use square footage more lucratively than it is right now, how to improve the facility.”
The decision he arrived at was to keep the building’s existing footprint but to expand vertically by increasing the height of the roof and installing taller racking equipment inside the warehouse.
“Originally the building was 14ft high. Now it’s 24ft. The racking is up to 20ft in height. Before it was 10ft to 12ft. So we’ve doubled it.
“We use the same equipment to reach it—we have forklifts—only now we’re using it more efficiently. We didn’t use our material handling equipment in its fullest capacity before. Now we are, and we can go high.”
Braunshtein says the former storage capacity topped out at 2,000 skids. Today the company is storing 2,500 with lots of room to add more.
After making the decision (in full consultation with company owners and executives) that raising the roof was the way to go, the company hired a contractor, Eugene Slutsky, who brought RoofLifters Canada Ltd into the project.
The Toronto-based company requested drawings of the CMS facility in order to prepare preliminary sketches and do projections about the scope of the renovation project.
Then, over the course of a few months, RoofLifters created detailed plans, performed the engineering calculations, got the building permits, and won approval from city hall for the renovation.
Before the construction started, Braunshtein spent a week moving all of the stock into another facility.
“I rented an adjacent building for storage during this period of time and transferred all the storage material and packaging material, everything I used to keep here, to the adjacent building. Freezers I had in another premises. I took everything out so when the building was free, we could work. I had to disconnect all electrical power supply, all security. Everything was disconnected. Then afterward I had to bring everything back. So it was a big job.”
CMS managed to keep its production lines operating during the entire operation, as they were in a separate part of the building.
The actual lifting the roof took about four months, as the RoofLifters process increases the height of the roof 15cm to 30cm (6in to 12in) per hour. [See below for details about the process.]
Once the roof reached its final height, the walls were built up to reconnect the roof to the structure. CMS opted for new brick to match the existing building. Internal systems, wiring and plumbing weren’t fundamentally changed.
“We didn’t have any problems. We made all the wires flexible, so we just straightened out the loops of electrical cables. They just straightened out and were put in the right place.”
The basic structure of the roof was kept the same although since the old roofing surface was leaking, a new surface was installed.
“It was a smart move because we improved the quality of our facility. We made a better looking building from the outside with better working conditions. We put in new lights, a new roof with a 25 year guarantee, new walls and it looks fantastic—a brand new building from an old one. I’m happy with it. Sometimes you waste your time and money, but in this case we didn’t.”
Braunshtein estimates that with the increased roof height, the value of the building has increased 25 percent. And he adds that when CMS is ready to expand and buy an additional facility, he’ll recommend looking for a less expensive building with a low roof and repeating the process.
The mechanics of roof lifting
Marty Shiff, CEO of RoofLifters Canada, describes what his company does in ecological terms: “What we do is we recycle older buildings. Rather than knocking them down and sending the materials to the landfills, we rebuild them.
“We recycle and reuse 90 percent of the materials in the building. All the walls remain, all the steel in the building remains, all the roof remains. It’s only being added to.”
The process of lifting the roof is pretty simple.
“What we do is separate the roof from the perimeter walls, shore up the outside walls and then raise the whole roof structure.”
And “raise” is exactly what Shiff means. Computer-controlled hydraulic hoists, known as cribposts, are set up beside the existing columns in the interior of the building.
“Once they all get pressurized, we are taking all of the load off the columns and transferring it to our cribposts. So once we’ve transferred all the load, we cut the columns. Then we are in control of that whole roof. They are all hydraulically controlled by one or two central control panels, and they will all go up at the same time.”
Then the steel columns get infilled after the roof reaches its final height.
“Depending on how high you go, you might be required to replace full columns. We don’t do any underground work. What happens is we’ll cut the column at about six inches from the top where it connects to the existing beam and girder structure, because that’s a tough thing to duplicate. And we cut it about an inch from the floor. We’ll actually slide a square column—an HSS column we call it over the existing steel, so it’s a steel-to-steel connection which transfers all the load down into the existing footing.
“The old roof just lowers back down onto the existing structure. So any of the sprinkler lines that were attached to the existing roof structure, any of the heaters, any of the lighting that was attached to the roof would go up with the roof lift and get reconnected at the higher height.” MM&D
Leave a Reply