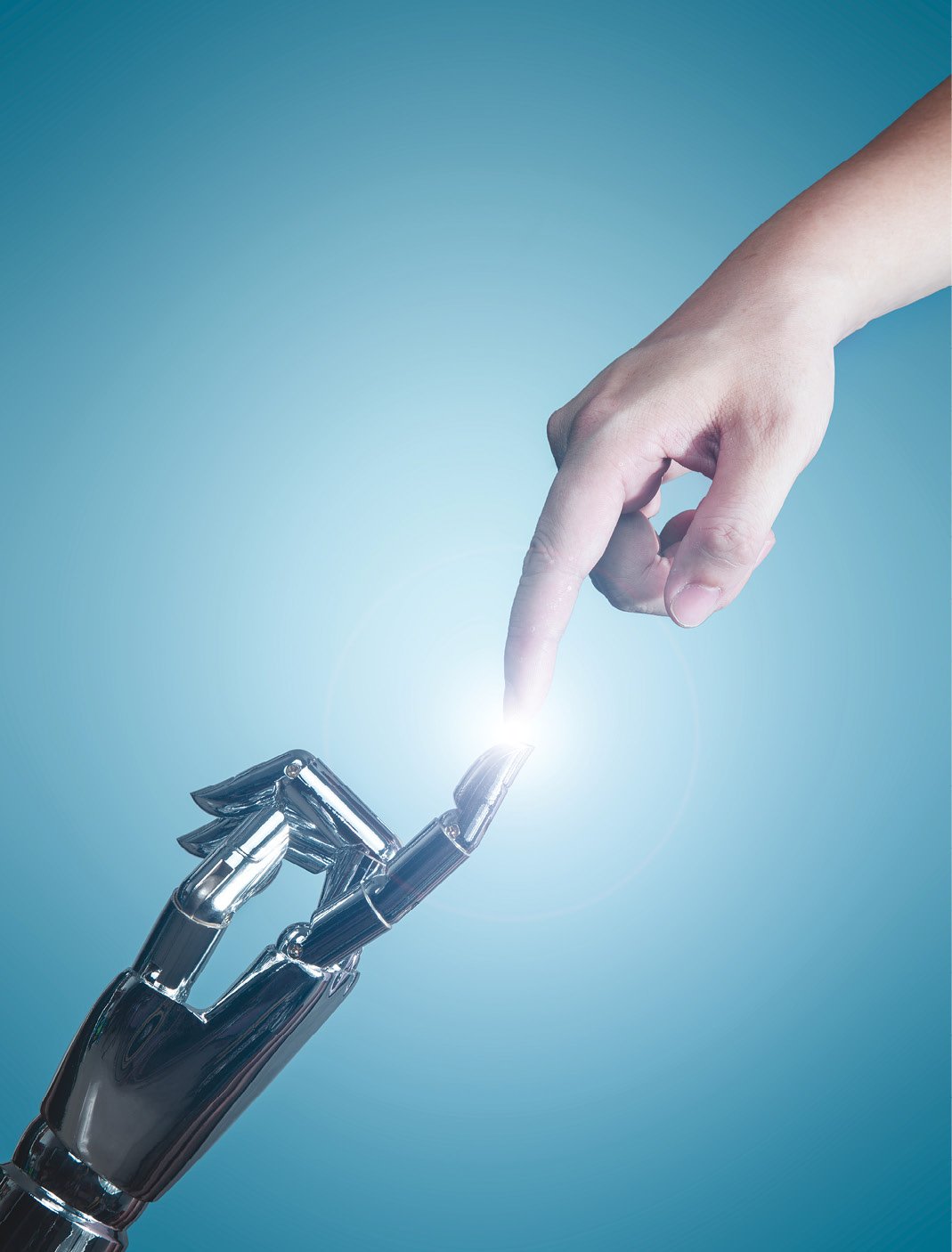
As supply chain operators look ahead, there’s guarded optimism that pandemic-triggered imbalances will stabilize in the coming months. A rebound in the labour market, however, seems highly unlikely.
“The people I’ve talked with believe that many of the pandemic-related disruptions will resolve themselves,” says Joe Campbell, head of Americas marketing and application development for Universal Robotics, Ann Arbor, Michigan. “But they’re starting to get a clearer understanding that the labour situation is not going to go away, and they’re not going to be able to wait it out.”
Many who left the workforce in the past two years are unlikely to return. “Part of what they’re calling the ‘Great Resignation’ is baby boomers who were at or close to retirement age,” says Campbell. “So as we go into year three of Covid, many of them have adapted their lifestyle to being retired, and they’re just not going to take the risk of going back to work.”
Unfilled job postings in warehouses and distribution centres, consequently, are the new norm as a growing number of Canadian companies hit a wall in their recruitment efforts.
“We have clients in Quebec that have virtually exhausted their ability to attract labour,” says Richard Kunst, president and CEO of Toronto-based Kunst Solutions Corp. “They have reached their ratio of foreign workers that they are allowed to have in their workforce, and their only alternative has been to go down the path of automation.”
Changing attitudes
Labour market realities are changing how people see robotics. “Years ago, everybody was scared that robots would come and steal jobs,” says Kristian Hulgard, general manager – Americas at OnRobot, based in Irving, Texas. “Now it’s a completely different mindset – companies are automating because they can’t find people to do the work.”
“The question is, how do we increase productivity enough that we don’t have to hire those extra people that we can’t find anyway?” says Kristi Montgomery, vice president, innovation, research & development at Kenco Group, in Chattanooga, Tennessee.
Warehouses and distribution centres, however, are tough to automate. Compared with manufacturing, logistics workflows are more variable and more volatile – more so since the pandemic has accelerated the growth of e-commerce, and an accompanying prevalence of high-mix low-volume activity.
What companies hope for is to reduce their dependence on temporary workers and at the same time, increase the productivity of skilled employees who do value-added work.
“We want to retain our core team and continue to invest in them,” says Montgomery. “But if we can augment that core team with tools like robotics that allow them to work smarter, and faster and better, that’s our goal.”
Automating amidst the growing complexity of supply chains will involve new skill sets on the floor. “The challenge is that this has created a whole new occupation within organizations, where before they never had departments focused on automation,” says Kunst. “How can I standardize my end-of-arm tooling to basically manage multiple products in similar processes without adding labour? And our traditional operator now has to have a much higher skill set, because they have to be able to problem-solve automation issues.”
Collaborative technology
Industrial robotics have evolved significantly over the past decade, opening up many more opportunities for automation. At the centre of the trend are collaborative robots or cobots that are designed to work side-by-side with humans and don’t require major investments in fixed infrastructure. Compared with traditional robots found in automotive plants and other mass production facilities, the newer technology is safer, more versatile, cheaper, and easier to implement.
This new paradigm allows warehouses and distribution centres to break down the automation juggernaut into a series of smaller incremental projects.
“I think the barrier to entry of automation is dramatically dropping,” says Kunst. “To take robotics for example, you can grab the end of a robot arm and basically take it through the motions of what you want it to do to replicate what a human being would provide, and the thing is programmed.”
The availability of solutions for logistics-specific tasks has exploded, with seemingly unlimited options for robotic arms, grippers, vision systems, smart conveyors, mobile robots, lift trucks, and transport vehicles.
Vendor solutions typically interact with workers on the floor, assuming physical tasks such as lifting and carrying, and providing guidance to help reduce errors and improve efficiency. “Robots like those from 6 River Systems guide associates through optimized pick routes, which reduces walking, eliminates heavy carts and limits human error,” says Fergal Glynn, VP of marketing at 6 River Systems. “Robots are the perfect fit for predictable tasks like moving items around a warehouse.”
Solutions to logistics problems, however, are by nature task-specific. “These products do a single task like picking very well,” says Montgomery. “But there’s not a single one that does everything well, so you’re going to need multiple solutions inside your four walls.”
Talking to each other
Working with multiple solutions saddles companies with the perennial IT challenge of managing multi-vendor data environments. The problem is that for a manager to have a single view of the operation, apps from different vendors have to be integrated.
Management software, accordingly, is a growing component of the product mix provided by robotics vendors. “Logistics and warehousing is extremely reliant on data – more than a lot of other companies,” says Hulgard. “So having a tool to give them that data from their robot application has shown to be a necessity. So we’re seeing a lot of growth in that segment.”
SVT Robotics, a software company founded in 2018, has developed a platform that allows employees with no programming background to connect robotics with enterprise apps such as Warehouse Management Systems (WMS) or a labour management system. This eliminates the need for custom coding – a process that can take weeks.
“It seems to me that the people bringing the value are the ones who are making the connections easier, and helping you augment and optimize the way those robots interact with each other,” Montgomery says. “It’s great if I have a great robot, but if my WMS can’t give that robot instructions that are detailed enough to be successful in the warehouse, then what value is it? So I need that software layer that can build that workflow.”
That software layer also makes it feasible to test multiple robotic solutions to determine the best fit, Montgomery notes.
People and processes
In addition to the technical issues involved, impending automation projects put pressure on managers to ensure their processes slated for automation are stable and efficient. If, say, a restocking process hasn’t been well developed and optimized before automating, even the best-designed project can have the effect of further embedding the deficiencies of that process.
Similarly, there’s no point in automating work that doesn’t need to be done in first place. “We tell our clients that they need to take five deliberate attempts to simplify the process before they automate it,” says Kunst, “so we’re saying simplify, simplify, simplify, simplify, simplify, and then automate.”
Planners also need to look beyond the local process and assess the overall impact of automating it.
“Let’s say I triple the productivity in my picking area,” says Montgomery. “What oftentimes happens is that creates a logjam somewhere else, such as your packout area. So I think one of the lessons learned for implementing robotics has been making sure that you’re really looking at your holistic supply chain processes within the four walls of the warehouse and making sure that the robotics are going to add to the whole process and not just a specific component.”
Safety matters
Safety is another fundamental that has to be wired into every project from the outset. Collaborative robots move at a slower pace and have reliable vision systems to prevent collisions, but they’re not perfect. Safety measures, therefore, need to be embedded in automated workflows. Assigning autonomous vehicles to dedicated routes where fewer people are present is one example.
Less obvious but equally important is the impact projects have on employees’ mental health. “I think one of the big risks of going down the path of automation is that we lose that social interaction,” says Kunst. “I’m seeing that in retail, and also in the warehouses. Will we become socially distant and not care about the work we’re doing?”
Issues like this call for ongoing dialog with employees on the floor. “You have to be open and transparent about what you’re trying to do with the robotics, and how it’s going to improve people’s lives,” says Montgomery. “Then you have to get them involved in the success of the tool by giving you feedback on a regular basis. What can we do better with these robots? How can we use them better? How can we change the way we do things with them to make things better for you?”
Leave a Reply