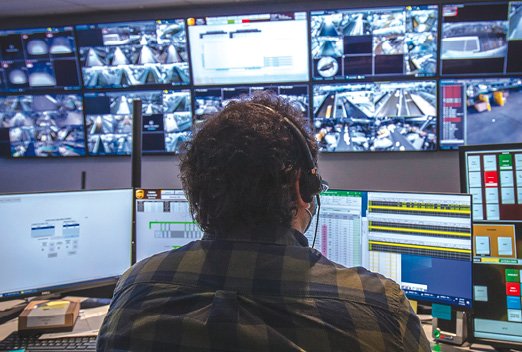
It’s like watching a child taking its first steps,” says Gordon Reed about seeing UPS Canada’s largest package sorting and delivery facility up and running.
As the director for special projects in UPS’s industrial engineering department, Reed has spent long hours working to get the massive, 850,000-square-foot facility in Caledon, Ontario, from a hole in the ground to operational. And, as if building a sortation hub wasn’t a challenge all on its own, UPS has had to cope with the Covid-19 pandemic during construction, and now, operations.
Located at Dixie and Mayfield roads on a 102-acre plot that used to be a corn field, the facility is an automated sorting hub and package centre – two operations under the same roof. It was conceived as part of a $500 million Canadian investment plan announced in 2018. Operations began in the final quarter of 2020 in anticipation of the annual increase in volume that started around Cyber Week in November and continued through January 2021.
The sorting facility handles about 100,000 pieces a night, taking in parcels from all over the UPS network. Inbound tractor-trailers arrive at 21 dock doors starting at 11pm, and are unloaded. Parcels are sorted and loaded again, either into the local delivery trucks or into truckloads that head for depots in other cities across the country.
Around 9 am every day, about 200 of the familiar UPS brown parcel vans leave, covering deliveries to addresses from Milton through to Brampton, and from Lake Ontario up to Orangeville. Soon, capacity will expand to 35 inbound doors and 116 outbound, once the second half of the building opens this spring, Reed says.

Pushing for the rush
A year ago, when Covid-19 was declared a pandemic, the building was under construction. And the deadline was to make it operational to handle the 2020 holiday rush. Pandemic construction shutdowns and subsequent workflow modifications to allow for physical distancing and safety protocols slowed construction, Reed recounts.
“We were shut for six or seven weeks where all construction was shut down in the province, and that obviously had a big impact on us,” he says. “Once we were able to open up again, there were days you never knew how many people were going to show up.”
They added additional portable washrooms everywhere, broke up lunchrooms to make smaller groups, and made sure tasks were organized to have people working independently whenever possible.
Once those measures were in place they were able to add shifts to spread people out, and were able to catch up from the shutdown. “It stabilized, everybody understands when to come to work, when not to come to work, how to protect themselves,” Reed notes.
A bigger challenge, however, was supply chain issues as a result of Covid. “Suddenly components are arriving out of order, out of time, we couldn’t get what we needed when we needed them and had to work around it. That took a lot of coordination. That was probably the number-one problem we’ve experienced.”

In-house automation
Reed calls the hub “state-of-the art”, and while many companies boast this of their facilities, UPS can genuinely make the claim. It designs the automation in-house, using the best from many disparate vendors to create systems unique to its operations, and standardizes them across many facilities.
“We do all of our own development, and then we hire contractors to essentially assemble it, and connect it to us,” Reed says.
“The nice thing about that is if I have problems, I can talk to any of my counterparts in any other automated building in the world, and we all speak the same language. So if I’m trying to do something to satisfy a customer, or a building, or a scenario, I can talk to others and say, ‘How did you do it?’, figure out what they did and then I can mimic that.”
In Caledon, human de-stuffers place parcels on automated conveyors that extend all the way into the 53-foot inbound trailers. That’s one of the few places where human hands touch the packages that flow through the building.
Conveyors then move the parcels to the mezzanine level of the 45-foot-clear-height building where they enter the sorter. The sorter automatically puts the boxes in a straight line, and gaps them so there’s at least six inches between each box.
They then go through a six-sided scanner that is reading where the box is going and its size. The system then knows which depot that parcel will be headed for and directs it accordingly.
A puck sorter takes the destination information and box dimension and shoots the parcel into one of 13 secondary sorters, which then direct it down to truck level. Once it reaches the outbound dock area, another human will take the parcel off the conveyor and load it in the right truck.
“When everything works perfectly, then the only two people who ever touch that box are the person who unloads it, and the person who loads it,” Reed says.
Low-touch, lots of hands
Although the sorting system is low-touch, UPS Canada employs 500 people on site. In addition to the loaders and unloaders, which are the largest crews in the workforce, there are the parcel van drivers and about a dozen mechanics and engineers who run the building, and an IT team of about five who keep the automation systems up and running.
For any facility that employs so many, getting to and from work can be an issue. Fortunately, Reed says the hub’s remote location has not been an issue. “Transportation links don’t exist,” he says. “The closest bus stop is almost a two-kilometre walk, so it’s not ideal. We’re the new guys in the neighbourhood, and the neighbourhood hasn’t grown up yet. But we have not had a significant issue getting employees.”
Expansion plans
While the Caledon facility is already the biggest in Canada, UPS built it with “no end date in sight”, Reed notes.
“When we build buildings, we want them to last a long time. We have the ability to almost double the capacity when the need arises. If you were in here, you would see gaps where there’s just nothing there. We’ve already planned additional sorters to go in. The basic infrastructure’s there, all the steel work’s in place, but today we don’t need that sorter, we don’t need the 21 doors that would have attached to them.”
The capacity expansion means being able to jump from 21,000 packages an hour at the time of opening late last year, to 35,000 this spring, and up to 58,000 in the future.
On top of that, Reed adds, they are also building an automotive shop. “We’ll be able to fix our own trucks, our own tractors, our own trailers. We’re putting in an automated car wash so we can wash our vehicles, and our own fuelling stations. Right now I can fuel propane on site, and in the spring I’ll also be able to fill gas and diesel vehicles.”
Reed notes he’s being conservative in promising the facility will be fully operational by the end of 2021, hinting that the end of Q2 is possible. But even then, the facility will remain poised for the future growth that UPS baked in from the beginning. “When we build these things, it’s very forward-thinking,” he concludes.
Leave a Reply