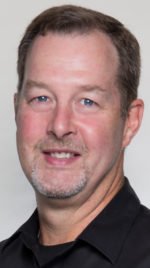
In October this year alone, the Canadian government warned consumers of 46 recalled items ranging from Halloween costumes to car parts and fresh, frozen and canned foods.
Recalls and regulation requirements touch every industry. Just one recall can cost a company an average of US$10 million, not including lost sales, profits and a tarnished brand reputation, according to a study by the Food Marketing Institute and Grocery Manufacturers Association.
In addition to recalls, manufacturers in many industries are facing increased regulations. These regulations have manufacturers searching for cost-effective solutions for increasing product traceability from the production line through delivery.
This is where manufacturers see the benefits of a warehouse execution system (WES). Connecting a WES to both upstream and downstream systems in the supply chain increases product traceability, allowing manufacturers to respond to problems within the manufacturing process more quickly, as well as ensuring that they are meeting regulation standards.
The WES and recalls
By providing a high-degree of product traceability, an integrated WES can help manufacturers more quickly discover and act upon issues that have caused the recall. Earlier detection often allows manufacturers to better understand what product is to be recalled, thus potentially reducing the scope of the recall effort by targeting only affected inventory.
For example, suppose a manufacturer ran a lot of a single product on a production line at midnight and then determined that there was a problem with those products. The manufacturing system can communicate to the WES and locate all of the products that were produced from that particular line during the specified timeframe. The quicker this response can occur the greater the chance that contaminated or malfunctioning products do not leave the facility.
If not caught before the products leave the facility, utilizing a WES that is tightly integrated with other supply chain systems allows manufacturers to more quickly and easily identify products to be recalled by showing:
- What vehicle(s) the products are on;
- Where the products are located on the vehicle;
- What specific stops occurred during transit;
- What other product(s) might have mixed with the contaminated products.
Companies can then use this information to provide their customers with the information needed to identify and return the recalled product quickly and efficiently, saving both the company and its customers time and money.
A well-managed process is crucial when processing recalled product accurately and efficiently. There are many different recall scenarios that a manufacturer must be prepared to handle.
What to do with the returned products? Should the products be discarded? Is special handling required? Do the products need to be quarantined for further inspection? Are there specific reporting requirements? Many of these processes are easily automated within a WES and will guide individuals through the process, ensuring a complete, well-organized, well-documented event and efficient handling of the affected product.
The WES and regulatory compliance
Increased regulations are requiring that many manufacturers are able to trace their products from production through to delivery at the retailer.
For example, increased traceability regulations in the pharmaceutical industry now require manufacturers to record every movement of each pharmaceutical produced. Now manufacturers must be able to trace:
- What time the product went into/out of specific controlled environments;
- What time and for how many minutes it was out of that environment;
- What time it was loaded onto the vehicle for delivery;
- How many minutes it was on the vehicle and at what temperature;
- What time product reached its destination;
- How long product sat in a particular location;
- What time the product was put back into a controlled environment at delivery location.
With complex traceability requirements such as these, manufacturers with a separate WMS and a separate warehouse control system (WCS) often run into traceability issues. However, with a WES, manufacturers can implement traceability and control requirements within a single solution and because the WES connects to other systems, the application can orchestrate the process across the entire supply chain.
Contaminated or malfunctioning products and regulatory non-compliance can potentially be hazardous to end customers. Certainly, they can be extremely detrimental to a company’s financial health as well. By integrating a tightly integrated WES into the supply chain process, manufacturers are able to implement traceability and control requirements throughout the supply chain and are able to quickly identify, track and efficiently recall contaminated or malfunctioning products when necessary – saving time, money and often their reputation.
Leave a Reply