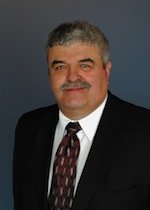
Greater Toronto Area.
Many factors make it sensible to increase the cube of your warehouse. The high cost of real estate, energy costs and building envelope costs all can be reduced with a smaller footprint and taller building.
In refrigerated warehousing, conventional (single deep) selective racking is a poor design option, except in unusual cases. Pallet storage is the dominant type of system used.
In a conventional, single-deep, selective racking system, storage aisles account for about half the usable space. Use of a properly designed high-density storage system can significantly reduce the space needed.
As a starting point, the system designer should remember that most of these systems achieve their success by eliminating storage aisles to greatly increase the amount of usable storage capacity.
However, this increase in capacity comes at a price, because as the storage capacity is increased the accessibility of the product for order picking is inevitably decreased. There is an ongoing conflict between the need for product access and the need to maximize storage capacity.
This inverse relationship between storage density and accessibility, often means that the successful deployment of most high-density storage systems is restricted to only part of the inventory items to be stored. Those items with the largest proportion of product per SKU in terms of pallets are the best candidates for a high-density storage system.
A related design issue is the amount and type of order picking that must be done. If only full-pallet order selection or handling is required, there is limited need for designated order-picking slots.
However in most full-case order selection systems, the efficiency of using picking locations accessible both at ground level and located right at the aisle is an important system design objective. Thus, many of these systems have order-picking at ground level with reserve storage at upper levels. Alternatively a forward picking area maybe used, in which the picking area is separated from reserve storage.
High-density storage
Common types of high density storage systems include: Bulk Pile or Block Storage; Double Deep Racking; Drive-in or Drive-Through Racking; Pushback Racking; and Flow Racking.
For a new or retrofit storage system, a designer should determine the number of standard unit loads high that can be stored vertically in the system. This vertical unit load or pallet piling capacity in turn establishes the maximum potential vertical cube design capacity of all available high-density storage systems.
Note that the vertical capacity varies between systems as two of them—pushback and flow racking—use a sloped rail to convey the pallet to the front of the rack face.
Double-deep pallet racks also require more clearance for damage-free handling, which may result in reduced vertical capacity.
While most high-density storage systems can use high-height warehouses because they rely on the racking, block or bulk pile systems are dependent on the stacking capacity of the pallets and the unit load contents. This usually limits the application to ceilings of 20 feet or less.
Fundamental differences between the way various kinds of high-density storage systems operate affect the practical capacity and selectivity of each system type.
In double-deep, pushback and flow racking the lift truck remains at the access aisle. For double-deep racking, a specialized lift truck with an extensible fork places the pallet into the second storage position. However the storage system is limited to a maximum of two pallets deep.
Pushback and flow racking are sometimes called ‘live storage’. These storage systems automatically index a pallet to the storage aisle once another is removed.
In block storage and drive-in racking the lift truck must make a right angle turn to the storage aisle and enter the storage lane or tunnel to retrieve stored pallets. This limits them to full pallet handling applications unless only a very shallow depth (two to three pallets deep) is used.
Both the intended function of the high-density storage system and its type influence the selectivity that can be accommodated.
For drive-in and bulk-pile storage the channel is the entire vertical tower that a lane or tunnel forms. For the other three systems, selectivity is increased by the number of vertical levels because each vertical storage level functions as a separate storage channel.
SKU analysis
For a high-density system used for case order-picking selection, determination of capacity focuses on the number of pallets of reserve storage compared to that required for order picking. A more refined SKU analysis is beneficial to see if part of the inventory would qualify for high-density storage.
Two data analysis principles can facilitate determining which items are logical candidates for deployment in a high-density storage system. In both, the key design output is the ratio of the amount of reserve storage to the required number of pallet pick face positions.
The first analysis employs “Pareto’s Law”, or the 80:20 rule. This focuses on the 20 percent of fastest moving items which make up 80 percent of storage requirements.
An ‘ABC’ analysis divides SKUs into classes; “A” items—the fastest movers; “B” items—the intermediate movers; and, “C” items—the slow movers. For high-density storage systems we are normally interested in the fastest movers.
One risk of deep storage lanes is honeycombing—unused space for pallets within the channels. To reduce this problem there should be three storage channels per SKU. This principle is true for all high-density storage systems and is used to help determine the proper depth of the high-density storage for each application—sometimes called the ‘rule of three’.
Block storage
Each high-density system offers a advantages and disadvantages. As an example, we will look at block storage, in which pallets or unit loads are stored directly on top of each other, without the use of support racking.
Block storage is a practical alternative in particularly if you have an older warehouse with relatively low ceiling height. The capital equipment needs are among the lowest of any storage system, but the building and operational costs are among highest.
Even so, there are a number of factors to be considered in optimizing a block storage layout. The chief factors include:
a. Determining your unit load handling needs internally and within the overall supply chain and selecting a design unit load size.
b. The tradeoff between the accessibility of stored loads and the storage density you require.
c. The best means for replenishing bulk products.
d. Maximum unit load stability and stacking heights.
e. Order-picking requirements.
f. Handling remnant or out-of-season lots.
Planning
We will illustrate how your planning might proceed with the first two considerations.
Unit load handling needs have an impact on travel aisle width and storage row clearance requirements. For standard pallet handling, the dominant influences are set by the turning and clearance needs of the lift trucks you’ll be using.
If your lift trucks handle large non-standard unit loads (for example, lawn or garden tractors), or in cases where load handling requires use of forklift attachments like carton clamps or forkless, top-handling (Basiloid) devices, special clearances for the lift truck and attachment combined are needed. In these cases check with your attachment supplier and/or lift truck dealer.
You should also run an ABC and Pareto analysis of SKUs to determine if a combination of short rows and longer storage rows gives you the most efficient layout. An advantage with a block is that short storage rows can be created adjacent to major cross aisles by turning the rows at right angles to the main aisle layout.
The big problem with block storage is changing trends in packaging and building design in recent years. Changing packaging design has reduced the use of rigid inner packaging—such as metal cans—which provided reasonable stacking heights, while at the same time warehouse building design has emphasized higher ceiling heights.
Thus the potential for wasted space if no racking support is used has increased. As well, the increasing use of recycled corrugated has resulted in sensitivity to high humidity periods where corrugated can lose half its stacking strength.
In addition to limited warehouse height, block storage—like most high-density storage systems—has the disadvantage of being a Last In first Out (LIFO) system. All other high-density systems, with the exception of flow racking, are also LIFO. That is why sizing of the system is important to ensure proper stock rotation. Design of the order-picking logic in the WMS system also requires careful consideration.
Like all high-density storage systems, block storage provides a variety of advantages and disadvantages to a warehouse designer. Collectively this variety gives good flexibility to reduce the cube needed to achieve a given storage capacity.