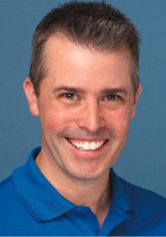
With COVID-19 fuelling explosive growth in e-commerce, now is the time to consider the role of ergonomics in machine/robotics safety programs. Otherwise, your workplace may be missing out on significant benefits.
Ergonomics and machine/robotics safety programs are not competing, as some workplaces may believe, but work in tandem to make the workplace safer and more productive, especially as warehouses and distribution centres try to keep up with the rapid growth in e-commerce. These changes may take the form of designing and introducing more productive equipment, machinery and processes. Collaborative robots are just one example.
Designing and introducing machines and robotic systems that meet the strengths of the people who operate them, which is what ergonomics is all about, can eliminate errors that may lead to injuries and costly downtime.
Identify hazards
I can’t overemphasize the importance of carrying out a risk assessment before modifying an existing system, designing a new process or purchasing new equipment. The assessment will help you identify and control ergonomic and machine hazards. Otherwise, you may be laying the groundwork for acute injuries and musculoskeletal disorders (MSDs), which can be costly to manage and result in lost time and productivity.
MSDs aren’t the only concern when ergonomic principles are not considered as part of a machine/robotics safety program. There is also greater potential for acute injuries. By ignoring ergonomics, workplaces may be reducing risk in one area, but increasing it in another.
Consider all tasks
Consider the potential consequences of not taking ergonomic considerations into account, after a worker removes a cumbersome conveyor guard because it gets in the way of completing a task.
During a risk assessment, you should consider all minor tasks (i.e. non-maintenance tasks) that are part of a machine’s intended operation. This ensures that safeguarding solutions protect workers from machine hazards while allowing access to necessary areas, and permit tasks to be carried out in an ergonomically sound manner.
Now consider a situation in which a high volume of goods has led to pallet loads left in aisles, forcing pickers to bend and reach around these pallets to access goods on racks.
Having to lift heavy items while reaching and twisting puts these pickers at high risk of MSDs. More effective inventory and storage practices can prevent injuries, keep aisles clear, and maximize productivity.
Six ways to build in safety
- Learn more about ergonomics and MSDs. Download the MSD Prevention Guideline for Ontario, which recommends a generic framework for preventing musculoskeletal disorders in the workplace. The framework is suitable for any Canadian jurisdiction.
- Get to know applicable standards, including: CSA Z432-16 – Safeguarding of Machinery; CSA B335 – Safety standard for lift trucks; CSA Z1004-12 – Workplace ergonomics; and CSA Z434‐2014 (ANSI/RIAR15.06‐2012) – Industrial Robots and Robot Systems.
- Ensure you have a strong risk assessment process to determine safeguards needed for every possible scenario. If you have or are considering robotic systems, consider bringing in an outside expert to help develop a robot-specific assessment.
- Involve internal and external stakeholders, including engineering, maintenance, health and safety, quality assurance, and even your contracted robotic systems integrator.
- Develop a checklist before you purchase to ensure equipment and devices have the right ergonomic features, meet the necessary requirements, and comply with standards and regulations.
- Train employees on safe work practices. Don’t wait for the pandemic to end. Virtual training options exist.
- Include robotic systems in monthly inspections to ensure robotic equipment continues operating safely, and to catch any hazards that may develop after installation.
Need help integrating ergonomics?
Download a free MSD hazards checklist. Visit http://wsps.news/MSDchecklist.
Watch a pre-recorded webinar on CSA-Z434-14, industrial robots and robot systems. Visit http://wsps.news/robotsafety.