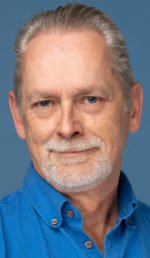
a consultant.
In today’s fast-paced, just-in-time workplace, imagine life without the lift truck. It’s difficult, isn’t it? Sometimes, it’s just as hard to imagine something going wrong. Maybe that’s because we haven’t experienced something going wrong, or worse yet, we don’t think it can happen to us.
In the blink of an eye, we can become a statistic. One of our workers gets injured, or worse yet, killed. A “jockey” at the wheel of the lift truck collides with a rack resulting in a multiple rack collapse. A supervisor turns a blind eye to the risks his operators are taking, just to get the product out the door.
A lift truck has all the possibilities of something going wrong unless we take appropriate steps to recognize how this might happen, and then implement the proper controls. Let’s examine a few thoughts:
Have we got the right equipment for our workplace?
We all know how expensive lift trucks are and we expect them to last a long time. And they do. However, the demands we place on the lift trucks change. We need greater capacity, to go higher, and faster. Sometimes the result is taking chances. It’s hard to place a ¾-ton load in a ½-ton pickup, or drive a semi in an area designed for a compact. Make sure the lift trucks match your workplace environment with an eye to future needs.
Do we have properly trained drivers?
How often have we heard “he can drive a car so he should be able to drive the lift truck”? Lift trucks are different and operators require special training – both theory and practical. Drivers need to understand what makes their equipment unique and to demonstrate their ability in operating it. Only properly trained and authorized drivers should be allowed to operate lift trucks.
How often do we observe operators to ensure they maintain that skill?
A well-trained operator is an investment because he or she will save you money due to fewer incidents, less product damage and greater overall efficiencies. And equally important, you need to train your supervisors as well. They need to know the laws, the equipment used in the workplace and how to properly manage a team of good operators.
Do we adequately control who operates our lift trucks?
“We have more than one driver of the lift truck so we just leave the keys in the ignition.” How many times have we heard or seen that? If you have more than one driver of the family car, would you leave the keys in the ignition? Sounds dumb, but I think I proved my point. Authorized drivers should be provided with a key, or install an electronic device to control who you authorize to operate your lift trucks.
Do we separate lift trucks from pedestrians?
Sidewalks, roadways, stop signs and traffic management are designed with a purpose – to make it safer for both pedestrians as well as automobiles. Do we try to do the same in our workplace? Free-for-all aisles and blind spots are a recipe for disaster. Consider implementing walkways, stops at intersections and pedestrian crosswalks. Take advantage of technology to help detect vehicle and pedestrian movement. Develop and implement a pedestrian safety program.
Do we hold staff accountable for safe operation?
When we observe a driver operating in an unsafe manner, or a pedestrian who fails to check at a blind intersection, do we correct that behaviour? Do we take time for that 10-minute coaching session? Are supervisors and managers held accountable to make sure they manage their staff appropriately? Are good drivers and pedestrians recognized and rewarded to encourage good driver behaviours?
Go home safe
Hopefully, we’ve highlighted some of the risks and factors that need to be considered to make sure everyone goes home safe at the end of the day. Although it’s hard to imagine life without lift trucks in today’s workplace, it’s even harder to recover from a disaster when it happens. They say “an ounce of prevention is worth a pound of cure” and nothing could be more true in today’s fast-paced workplace.