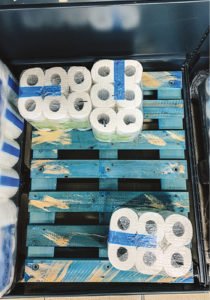
One of the many realizations from the Covid-19 pandemic is that our supply chains are a matter of life and death for many Canadians.
“I do think most companies and most supply chain leaders take this very seriously,” says Jeanette Barlow, vice-president, strategy and offering management, IBM Sterling Supply Chain Solutions, “and I do believe that as we emerge, post Covid-19, there is going to be a realization across every industry how fragile and yet critical supply chains are.”
“The word supply chain was never a ubiquitous word until this Covid pandemic,” says Robert Martichenko, founder and CEO of LeanCor Supply Chain Group. “Now everybody’s heard the term supply chain.”
The crisis finds many supply chain managers in firefighting mode as they adjust to the upending of retail shopping by stay-at-home mandates. Emergency home and curbside delivery setups have instantly transformed e-commerce from a convenience option to the predominant delivery method for groceries, hardware, office supplies and other verticals – a stage that wasn’t expected until years down the road.
“If you look at forecasts for where online grocery is going to go over the next two, five and 10 years, we just got a big stress test to the fulfillment systems and online capacity,” says Vince Martinelli, head of product and marketing, RightHand Robotics Inc. “It’s like we jumped ahead five years overnight.”
Simultaneously, supply chains are facing staffing shortages and unprecedented demand volatility.
“We’ve seen the whole gamut,” says Russell Kushner, senior engagement director, professional services at supply chain software provider Manhattan Associates. “We’ve seen folks that have their DCs go to almost zero volume overnight because their stores are closed. We’ve also seen people with major spikes.”
“It’s an odd time where certain things are moving at a hundred miles an hour, some things have come to a grinding halt, and others are, somewhere in between where they could accelerate or decelerate on a day’s notice,” Martinelli says.
Getting in focus
Many of the most visible problems, however, are not really shortcomings in the supply chain. The toilet paper fiasco, for example, occurred because consumers, afraid stores would close, began hoarding, causing widespread stock-outs. Shortages of masks and sanitizing wipes stem from manufacturing capacity issues.
Relative to a healthcare crisis, therefore, it’s unfair to attribute these problems to poor supply chain management. “We shouldn’t hold them accountable,” says Martichenko. “From a supply chain perspective, it’s not possible to know what to store, how much to store, where to store it.”
What’s needed is a broader way of looking at the many variables that can adversely affect a supply chain.
“Supply chain risk traditionally meant was ‘what is our risk of supply being interrupted?’” says Martichenko. “But what we’ve realized with Covid is that it wasn’t about interruption – it was about demand for some companies going through the roof, and for others, demand just dropping. So the supply chain wasn’t interrupted at all – the interruption was a function of demand.”
The question, therefore, is not “how can we make sure we have enough hand sanitizers?” but “how can we prepare so that we can quickly adjust to dramatically different circumstances?”
Tagging onto existing trends
Fortunately, the adaptive supply chain has been in the works for some time. The conversion of retail outlets to curbside pickup points, for example, leverages existing tiered network strategies where large DCs are supplemented by micro-fulfillment centres that provide same-day delivery of high-demand items to urban customers.
“I think what we’ve been seeing is a shift in facility automation and process flow,” says Crystal Parrott, vice-president of customer service at software provider and system integrator Dematic.
“Traditionally you’d have big DCs and they would send to the stores. What you’re seeing now is the move to a lot of smaller hubs closer and closer to the customer. You’re not eliminating the DC, but you’ve got the instant order facilities that have to be closer.”
To achieve this, many companies will have to upgrade their data-handling capabilities. “The challenge has been, I believe, that there’s so much data that you have to pull together,” Barlow notes. “It’s easier to do that within your swim lanes of particular processes, but to get that end-to-end view, you really have to be able to look across your own internal systems.”
A key advantage of this multi-layered distribution model is that it provides a degree of flexibility that many traditional retail networks have lacked. “That’s a sophisticated network of stuff to manage,” says Martinelli, “making sure you know where all the inventory and resources are – but it gives you a lot of flexibility to adapt as the demand bounces between the different ways that people may want to buy and receive things.”
Some companies are finding that they are already equipped for this, at least from a data perspective. “The customers that we see as the most able to react have flexibility built into their systems,” says Kushner. “We had a customer that was actually able to turn their stores into fulfillment centres in under two weeks.”
Coping with volatility
The crisis has also forced companies to adjust instantly to huge spikes in demand. By way of comparison, Martinelli points out, companies spend months planning for the holiday rush. “As warehouses get ready for Christmas peak and the holidays, they don’t wait until Black Friday to see how facilities operate and how the systems are going to hold up,” says Martinelli. “They usually do stress testing in June.”
Artificial intelligence is raising the bar here. Control tower technology, which monitors conditions and events across complex supply chains, can enable a decision maker to adjust to a pending shortage, or re-direct shipments to meet a spike in demand. Machine learning systems can evaluate multiple delivery models, automating a chore that would otherwise take months of work.
“Most companies have found an inventory model that fits their demand profile best,” says Kushner. “They might, on an annual basis or every quarter, review it and ensure that they’re using the right model. But when you get these completely out-of-the-blue changes in demand, your inventory model could potentially lag. So having systems that can evaluate multiple models in real time and adjust them is, I think, really critical.”
“It’s like an air traffic control mentality,” says Martichenko, “and I think organizations are going to be embracing that so they get the visibility they need, so they’ll have the capability and the resilience to see through these emergency events.”
Handling the goods
The crisis has also highlighted how quickly robots have established themselves in warehouses and distribution centres.
“Piece-picking robots for warehouses have only been around for three or four years,” says Martinelli, “so it’s kind of interesting that we’ve gone from brand new exotic technology to something that’s essential during a pandemic.”
This does not mean, however, that fully automated “pandemic proof” facilities are in the works. On the contrary, the automation that involves the handling of physical goods depends on humans for the kind of adaptability that is most needed in a crisis.
For example, put walls – which can be rapidly implemented to facilitate high-velocity batch picking of in-demand items such as toilet paper – deploy pick-to-light technology to help humans collaborate on the fly with machines.
“If you’re supplying paper towels and toilet paper,” says Kushner, “and all those things that are high demand, the ability to quickly enable temporary fast-moving slots and new pick strategies helps companies deal with these enormous spikes for critical and essential goods.”
The key is planning in advance so these alternate models are ready to implement in the time of a crisis.
“The people that have taken the time to design multiple processes and have that flexibility,” says Kushner, “definitely have advantages. They’ve got automation, which they obviously want to maximize. But at the same they have manual processes configured and ready to go. It’s about using the intelligence of your warehouse management system and just good old-fashioned management on the floor –
the ability to start orchestrating work across these different processes.”
“The more automated a warehouse is, the less flexible it actually is to scale up and down,” says Martichenko. “So an automated warehouse can be highly efficient relative to the volumes it’s designed for. But if volumes go below your plan, it’s going to struggle, and if your volumes exceed what it was designed for, it’s really going to struggle. So you get some emergency situation like the Covid pandemic and your highly automated distribution centre is not going to flex for that event. But a distribution centre that is being run by and large by people can certainly flex in both directions.”
Robots also, typically, can’t be deployed as a reactive measure – the widely discussed Robotics as a Service (RaaS) model is currently only feasible for clearly defined tasks such as welding.
“Automation projects in general take time to happen,” says Martinelli. “The manufacture and shipping of robotic picking systems won’t be the slow step. What takes some time is to integrate them into the overall automation scheme of a facility.”
Adjusting to the post-Covid-19 era
A likely outcome of the crisis will be that many who have tried e-commerce in the past weeks will stick with it. As Parrott explains, the pandemic has forced people who would never have been targeted as candidates for online ordering and delivery options to embrace them.
“The demand for individual online ordering, specifically in grocery, is a perfect example,” says Parrott. “After this is all over, all of these folks who would never have used the online tools to begin with are now comfortable with them.”
Another is that the supply chain profession may gain the respect that many feel it has been denied. The crisis has shown that supply chain professionals have a unique visibility into the wide range of corporate risks, even when such factors are not within their area of accountability.
“I think supply chain management is now going to be a very visible discipline,” says Martichenko, “and organizations that have not taken supply chain management seriously as a true operational discipline are going to say they need to get smarter and more professionalized. Training and education in supply chain I believe is going to be a very common curriculum now.”
“As companies emerge from this, I think people will be saying ‘never again – we are not going to be caught unprepared,’” says Barlow. “I think you’re going to start to see some real decisions on how they look structurally at their supply chain and how they can sort out their points of vulnerability, which will be coupled with a palpable understanding that now is the time to innovate and invest in systems that leverage significant technological advances such as AI to harness that data to gain a competitive advantage.”
“The big thing we’ve all learned is that our supply chains aren’t ready for emergencies,” says Martichenko, “and that we need to understand the risk associated with our supply chains, and we need to embrace supply chain management as a serious profession, where your executive supply chain is at the table in the boardroom.”
Leave a Reply