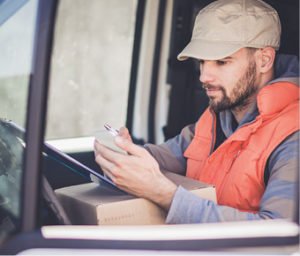
A typical delivery to a distribution centre can involve six exchanges of paperwork. And while paper itself has not been identified as a major culprit in Covid-19 transmission, preventing the spread of the virus by avoiding person-to-person contact is a high priority for most organizations.
Back in April supply chain consultancy Gartner was pushing the logistics industry to adopt new tech in aid of social distancing. “Technology solutions help reduce physical contact to a minimum. Routine procedures like gate check-ins and paperwork signing can move to the cloud via a software-as-a-service (SaaS) solutions. Real-time transportation visibility platforms flag shipments carrying essential goods, so staff can already prepare with protective gear, such as face masks and be in place to retrieve or offload quickly,” said Carly West, director analyst with the Gartner Supply Chain Practice.
“Proactive alerts are also a good practice for the last-mile delivery to end consumers. Tracking technology allows them to see when the delivery is approaching their home, as well as when it has arrived.”
This need for new best practices has led to a flurry of software development in the months since the pandemic disrupted supply chains around the world. Examples of new contactless apps abound, from body temperature sensors, to voice-enabled ‘signatures’ for home deliveries, to machine vision that can determine if someone is wearing a facemask.
“People want to get away from paper,” says Greg Braun, senior vice-president of sales and marketing at Montreal-based C3 Solutions, which makes yard management and dock scheduling software.
Paper typically changes hands six times on average, including when the driver arrives at the gate where the guard verifies paperwork, then at the receiving office for a second verification, and when the papers are transferred to the receiving staff in the warehouse and then back to the driver, who must interact another time with the gate guard before leaving, Braun notes.
That’s why people “want to be able to have a driver self-check-in, and avoid all contact with paper. And they want to be able to social distance from the drivers.”
As Inside Logistics reported last issue, students at Conestoga College have developed a geofencing app that creates an alert when drivers get within a certain range of the DC’s yard. That allows for door assignments to be issued via the app, rather than through a face-to-face conversation.
Other examples of such contactless yard and dock management have been introduced by visibility platform supplier FourKites, which has an ‘advanced mobile package’ that includes electronic proof of delivery (ePOD) and electronic bill of lading (eBOL) so that transportation workers can process all applicable paperwork on their smartphones from start to finish. Drivers will no longer have to manage physical paperwork.
“We are very excited about…the ability to manage documents electronically at the various pickup and dropoff points along our routes,” said George Henry, senior vice-president of logistics at USA Truck, a FourKites customer.
“This will significantly improve long-standing documentation problems related to payment and proof of delivery, and it will also help to provide a much-needed safety buffer between drivers and warehouse staff.”
Braun notes that C3 Solutions also offers paperless deliveries through its dock scheduling app, and will be offering automated check-in in the new year.
Keep-away technologies
(With files from John G. Smith, Today’s Trucking)
A few examples of new technologies being used to ensure physical distancing:
Eyesight Technologies has updated its driver monitoring system to detect the use of facemasks – adding to features that detect whether drivers are holding cigarettes or cellphones when they should have hands on the wheel, or track eye and head motion to detect drowsy or distracted driving.
Using fleet telematics information for contact tracing. “Testing and contact tracing are going to be critical to fending off a second wave,” said Fleetmetrica CEO Ward Warkentin. “Trucking is in an excellent position to use your onboard recorders, or ELDs, or telematics.” The added advantage is that the fleet data is already collected independently of personal details about a truck driver or a reported illness, so there’s no potential for a privacy breach, he said.
Using already-installed workforce visibility apps to ensure safe physical distances are maintained in warehouse environments. Triax has introduced ‘Proximity Trace’ which uses sensors worn by workers to provide audible and visual alerts when they are too close to another employee. The devices also continuously record close interactions, in case there is a need for contact tracing.
Leave a Reply