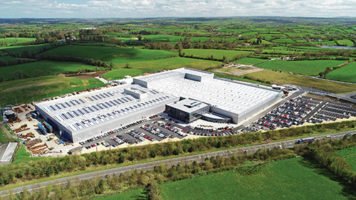
ANNAHAGH, MONAGHAN, IRELAND – At the end of April, Irish forklift manufacturer Combilift celebrated its 20th anniversary in business and the grand opening of a new production facility. The event was marked by a massive celebration, including supply chain media from the many countries around the world where they sell their product. Inside Logistics was delighted to accept the invitation to see Combilift’s new home and meet with managing director Martin McVicar to learn about the company’s plans.
Mass customization
McVicar was clear about the manufacturer’s focus: “Mass customization is the new frontier for both the customer and the manufacturer,” he said. “Increasingly, customers are expecting products to be tailored to meet their needs…Combilift is setting the benchmark by offering the mass production of tailored products…We evolve with our clients, producing new products each year.”
The factory, situated on100 acres of land, includes 500,000 square feet of production space.
In producing “bespoke” forklifts, the company works closely with customers in the design of machine and the warehouse it operates in alike. “We’re not interested in developing regular forklift trucks that have to compete with Toyota, Mitsubishi, Nissan, etc.,” McVicar said. “So, in the segments we enter, we want to become the number one player in that market segment within a five- or 10-year period, maximum.”
The venue for this mass-custom production is Combilift’s new 500,000-square-foot, light-filled factory situated on 100 acres outside the small town of Monaghan, Ireland. Processes on the shop floor are entirely manual, which McVicar says will allow flexibility to produce the high volume of customized forktrucks their customers are seeking. In fact, the set-up will allow Combilift to double production to meet future demand.
How it started
Founders McVicar and Robert Moffett (now technical director) established the company in 1998, building the world’s first multidirectional all-wheel drive internal-combustion engine forklift. In its first year of operation, Combilift produced 18 units, 17 of which were exported. There’s a Canadian connection: One of Combilift’s first customers was Toronto-based building products supplier Lansing Buildall, which bought a unit in 1999. To this day Combilift exports 98 percent of its production to 85 countries around the world.
The founders saw a niche market for long-load handling and for the first 10 years, the company focused on this market, selling to lumberyards, pipe manufacturers and the construction industry. The Combilift truck’s ability to essentially turn around the load instead of turning the load around the truck meant long products could be carried lower to the ground, and not lifted over people, machinery and other product in the yard.
“The Combilift multi-directional forklift revolutionized the handling of long materials as it allowed customers to handle long products in less space more safely,” McVicar said.
Building the niche
Over the first 10 years, the company developed this niche, launching one or two new products a year. But in 2008, with the economic downturn, the construction industry went quiet. This was the catalyst for the company to look for new markets, McVicar noted. As e-commerce was in its early stages, they saw the need to make better use of warehouse space and turned their sights to indoor forklift products.
Between 2008 and 2018 Combilift diversified its product range by developing products for the warehousing and heavy handling markets. For warehouses and distribution centres the company first built the Aisle-Master articulated truck that is designed to operate in a very-narrow-aisle environment.
In the past five years Combilift has gone deeper into this market, designing pedestrian forklift trucks with the introduction of the Combi-WR (walkie-reach truck) and Combi-CS (counterbalanced stacker). These trucks may be used in a 72-inch aisle as the operator and the controls can pivot to the machine’s side, allowing it to fill the aisle. Combilift has patented what it calls the “multi-positional operator tiller arm” technology that allows the pivot.

In the heavy-handling market Combilift builds the Straddle Carrier (Combi-SC), along with a variety of massive custom machines for unique applications. These are monsters with capacities up to 100,000kg, and many are remote-control enabled. They are all custom-designed, and are used to move items like wind turbine blades, aircraft engines and concrete tanks.
Most recently – at the anniversary event – the company introduced new members of the family, an order picker for long loads, and a high capacity powered pallet truck that can handle loads of 3,000 and 6,000 kg with higher capacities available on request.
Export markets
The company has more than doubled in the last five years and now has 40,000 machines in operation in over 85 countries. Last year it produced 5,000, 1,200 of which were exported to Canada and the U.S. More than 12,000 Combilift machines are operating in Canadian and American businesses, McVicar said.
While Americans are very gung-ho from the outset, “our Canadian clients are a bit more cautious in terms of new products, but I have to say when you win a Canadian client, you win them for life,” he noted.
“It’s for the simple reason that it’s a forklift that goes sideways, and it’s very easy for operators to understand,” said Paul Short, the company’s North America president. We have “a lot of operator acceptance, it’s so versatile, and has so many uses for big-box merchants, it’s a great tool for them to use all over.”
Another advantage is the ease of maintenance. Although the company has a parts depot in South Carolina, you don’t need exclusively Combilift parts to keep operations moving. “A lot of our major components are available in North America, so all of our hydraulic hose lines, either they’re standard so a customer anywhere in Canada can go to a local hydraulics shop, can get a hydraulic hose line made,” McVicar said. “A competent car mechanic can repair a Combilift anywhere, it doesn’t matter where in Canada, even in the most Northern territories.”
He points out that the company deliberately intends to keep it simple, but innovative, without relying extensively on complex electronics.
Combilift is counting on continued growth from our side of the pond. The aim is for sales of 1,600 units this year, a 30 percent bump from 2017, but McVicar notes they have already surpassed 36 percent growth year to date. He’s confident it will continue apace.
One fly in the ointment could be the Brexit. But McVicar’s not outwardly worried. Although there’s a “high probability” of tarriffs and import and export duties, the WTO tariff rating on forklift trucks is 4.5 percent. When you crunch the numbers, with the average client getting an ROI in 24 to 36 months, “even with that tariff of 4.5 percent, we don’t believe it’s going to have a major impact on our business going to the UK, but it’s going to mean our UK clients are going to be paying 4.5 percent more,” he said. “We’re going to have to deal with it when it happens, because I think none of us knows exactly what’s going to happen there either.”
Inside the factory
The new 46,500 square-metre purpose-built factory has 11 acres of roof space, making it one of the largest manufacturing operations under one single roof in the Republic of Ireland. Everything about it is carefully designed and looking to the future, from the shape, to the ability to reconfigure sections to accommodate growth.
McVicar explained the logic of the L-shaped design (see aerial photo). “Most production plants you see across the world, the best are the rectangular shape. The reason we developed in an L shape, [was] we wanted the administration block to be in the center of the L, so that for design engineers to go to any part of the shop floor people don’t have to walk so far.”
In the main stores area, where parts are held, the roof is peaked and well clear of the 40-foot racking. When asked why, tour guide Graham Moffett, normally a Middle East sales rep for the company, explained that when it comes time to grow the main stores will be moved to portable storage adjacent to the new building, and the current storage area will be converted to production. In the meantime, however, the warehousing section of the factory has 2,600 pallet positions, and a vertical carousel to manage smaller items.
They serve both the production line and repair orders from this location, with 92 percent of outside parts orders filled the same day. A part will be pulled from the production line to get an existing customer’s truck up and running faster, Moffett said.

Incorporating the latest manufacturing processes with a focus on sustainability, the new factory will enable Combilift to double its output in a single shift across all production lines. Four 90-metre moving assembly lines produce a finished truck every 15 minutes. Each line specializes in a type of truck. Every truck gets about 11 hours of testing, and they correct, on average, five or six defects per truck.
The company spent 16 months developing its own water-based paint, to reduce the overall VOC (volatile organic chemicals) emissions. According to Moffett, fully 11 percent of the factory is dedicated to R&D.
Thirty percent of its roof space is covered in skylights, enabling staff to work in natural daylight without the assistance of artificial lighting. LED lights with individual motion sensors are at the ready when it’s gloomy outside. Solar panels supply 185 kW of energy, while a 1 MW Biomass plant fuelled by recycled wood (pallets etc) provides heat for the painting booths and assembly area.
More than 50 truckloads of finished products are dispatched to 85 countries each week. Spare parts are also shipped across the world from Monaghan to the dealer network.
The new headquarters and manufacturing facility have been awarded ISO 9001 international quality management system, ISO 14001 Environment Management and OHSAS 18001 Occupational Health and Safety Assessment Series.
Staffing challenges
McVicar noted that the company deliberately spends 10 percent of revenues (currently at US$280 million) on its workforce. “If we can keep our labour content within 10 percent of that, we believe we can be competitive exporting anywhere around the world, because if we move this plant somewhere else, all we’re going to make the saving on is that 10 percent, and when you’ve expertise here, it’s not even something to consider,” he said.

And although the town of Monaghan has only 7,000 residents, with an unemployment rate of six to seven percent, the company has not needed to advertise job openings. McVicar says that being in a rural area means that many prospective employees come to the company with mechanical knowledge gained growing up on farms and working on the equipment.
Being close to the Northern Ireland border gives Combilift another concern about Brexit. With 52 staff crossing the border daily from Northern Ireland, “when the Brexit vote took place in June 2016, our biggest concern was employees, that there’s no big inconvenience at a border crossing,” McVicar said. Fortunately an agreement was reached late last year that will prevent a hard, physical border on the island.
“It gives our employees great comfort that there’s not going to be inconvenience getting to and from work. And, because as our business continues to grow and scale, if you draw a circle of where we are, we are going to be recruiting more people from northern Ireland, so we’re comfortable that there’s a solution there,” he added.
Since they began work on the new factory in 2015 the company has added 230 positions, and now employs 550. This number includes 50 staff in North America, and eight to 10 engineers solely dedicated to warehouse design – a service Combilift provides for free to customers. The rest working at HQ are skilled technicians, design engineers, logistics and supply chain specialists and mechanical and electrical mechatronics specialists.
Collaborative design
Combilift prides itself on taking a collaborative approach to design, both of products and facilities. As noted, warehouse design is offered as a free service to clients and prospects.
“We offer the 3D warehouse design service free of charge because we’re confident that our product’s going to bring our customers value, and we’re willing to take the risk to do the drawing without an order because we believe it’s going to demonstrate to the customers the value it’s going to bring,” McVicar said. “It’s an investment we’re willing to make up front, and it’s paid off over the years for us.”
Sales staff will map and model a customer’s existing facility over to a narrow-aisle design and use it to show them how much they might save by converting (a number they claim can be close to 24 percent more pallet positions.).
The company invests as much as seven percent of revenues into R&D each year. They work closely with clients to tweak existing products and blue-sky new ones.
For example, McVicar notes that the explosion of cold storage in North American is a new niche they are exploiting. “We’re very successful is in the cold store industry, because the cost of building a cold store warehouse, running it, managing it, is about three times the cost of an ambient warehouse, so we’re finding any company that’s looking to build cold store warehouses is really serious about going the Aisle-Master route.” (For an example, see our feature on the cover of the January-February 2018 issue on Ontario Refrigerated Services.)
To adapt the Aisle-Master to cold environments, Combilift engineers brought in a group of customers to modify the truck. They ended up adding heated cabins, replacing glass with a double-layered, heated, unbreakable polycarbonate, then fine-tuning the design to allow barcode scanning through the windows when they discovered the heating wires were interfering with the readers.
“Some of this might seem small, but we’re willing to go down into the detail to make it easier for the customer,” McVicar concluded.
Leave a Reply